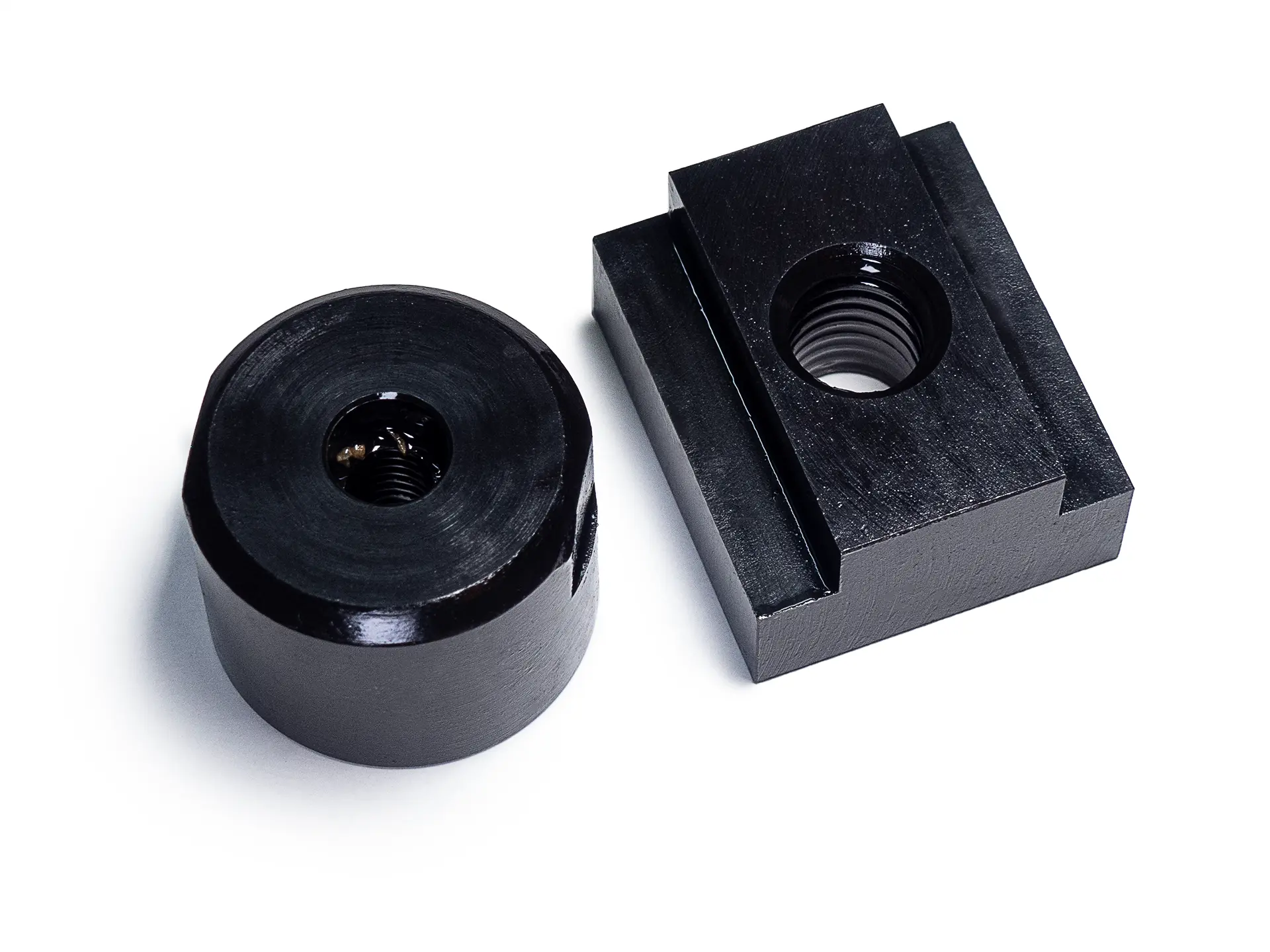
Bluing iron and steel quickly and easily yourself
The benefits of burnishing
- Easy DIY application
- For steel, iron, cast iron and zinc
- Price-performance ratio
- Reduces corrosion
- Creates even blackening
- Converts surface into oxide layer
Simple application
Burnish surfaces yourself
Flexible fields of application
How to achieve a perfect immersion bluing with the "Black Devil" set.
The process of our Black Devil bluing set is optimised to give you consistently good results when blackening larger objects by immersion/dipping. This is achieved primarily through the supplementary set components for pre- and post-treatment of the given workpiece. The essential process steps are as follows:
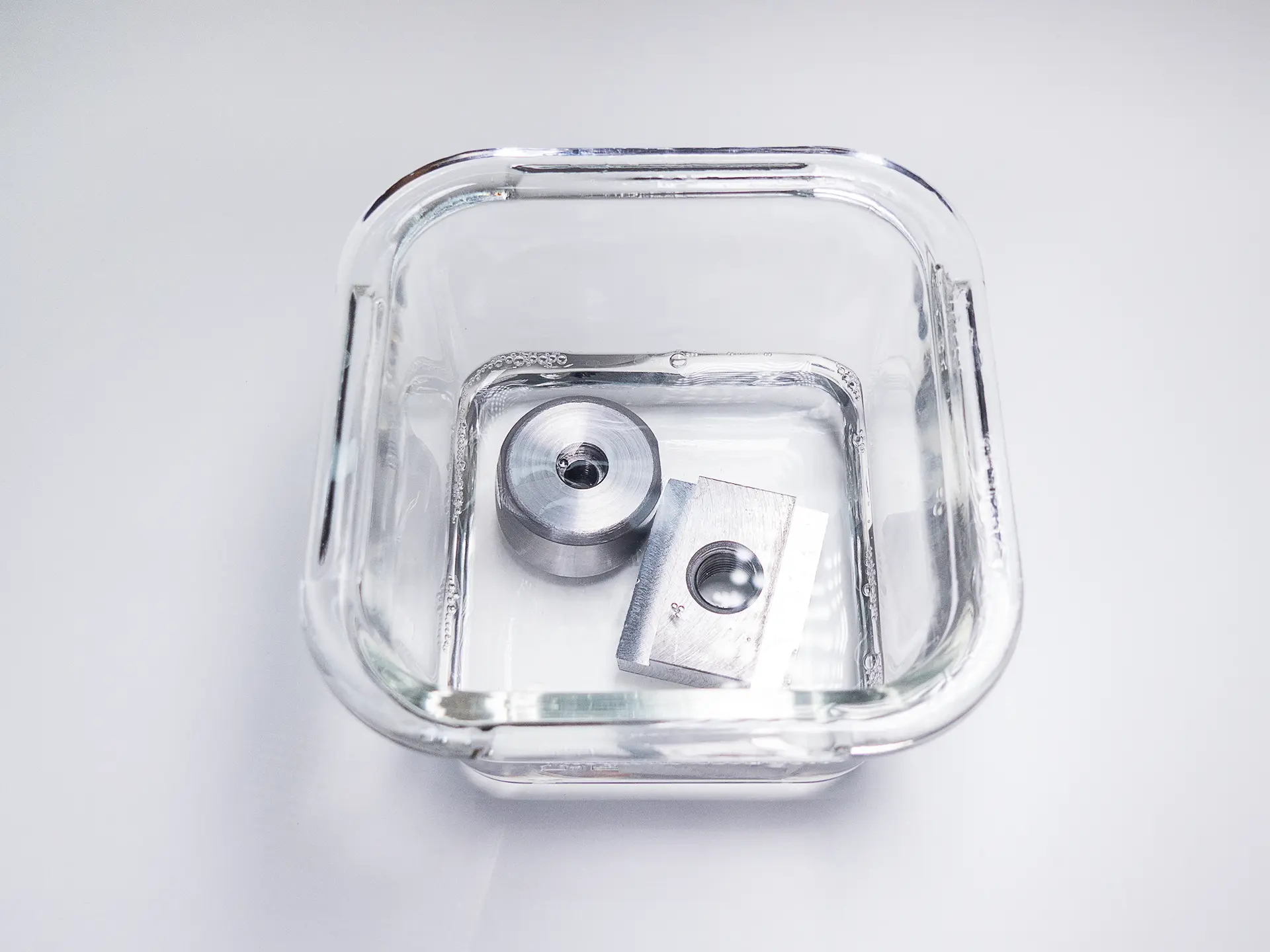
DEGREASING: Thoroughly degrease the item to be blackened with component I. Cleans from smear traces and grease residues that would impair the bluing result.
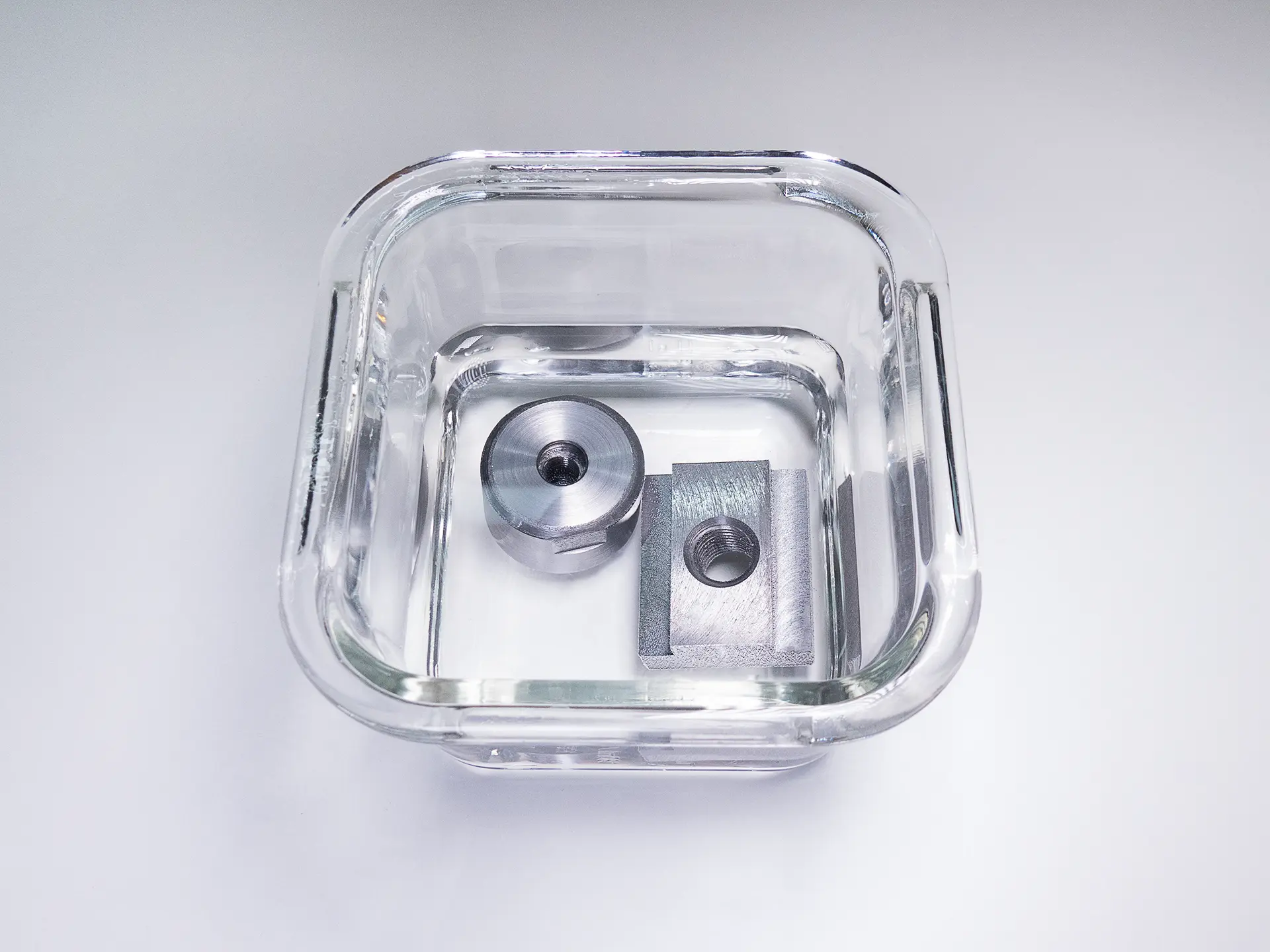
CONDITIONING: Treat the workpiece with component II after drying. This accelerates the bluing process and ensures a better result due to the surface activation.
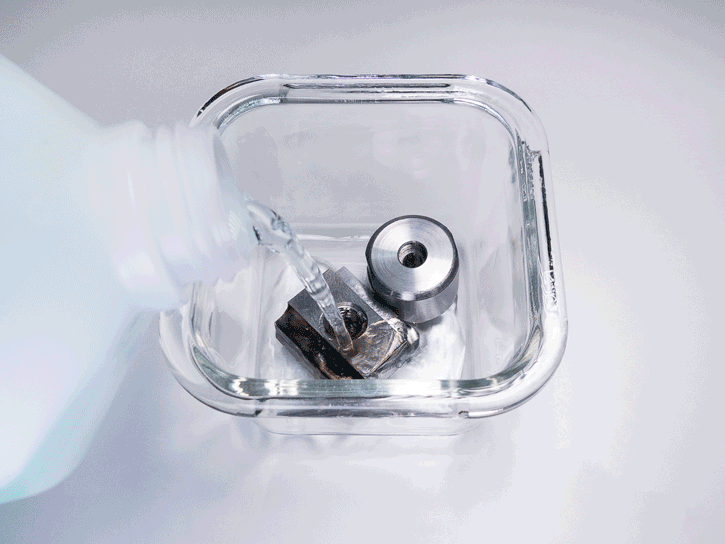
BLUING: Immerse object in component III for the respective duration indicated. Blackens the surface evenly and protects the steel surface. Repeat step, if necessary.
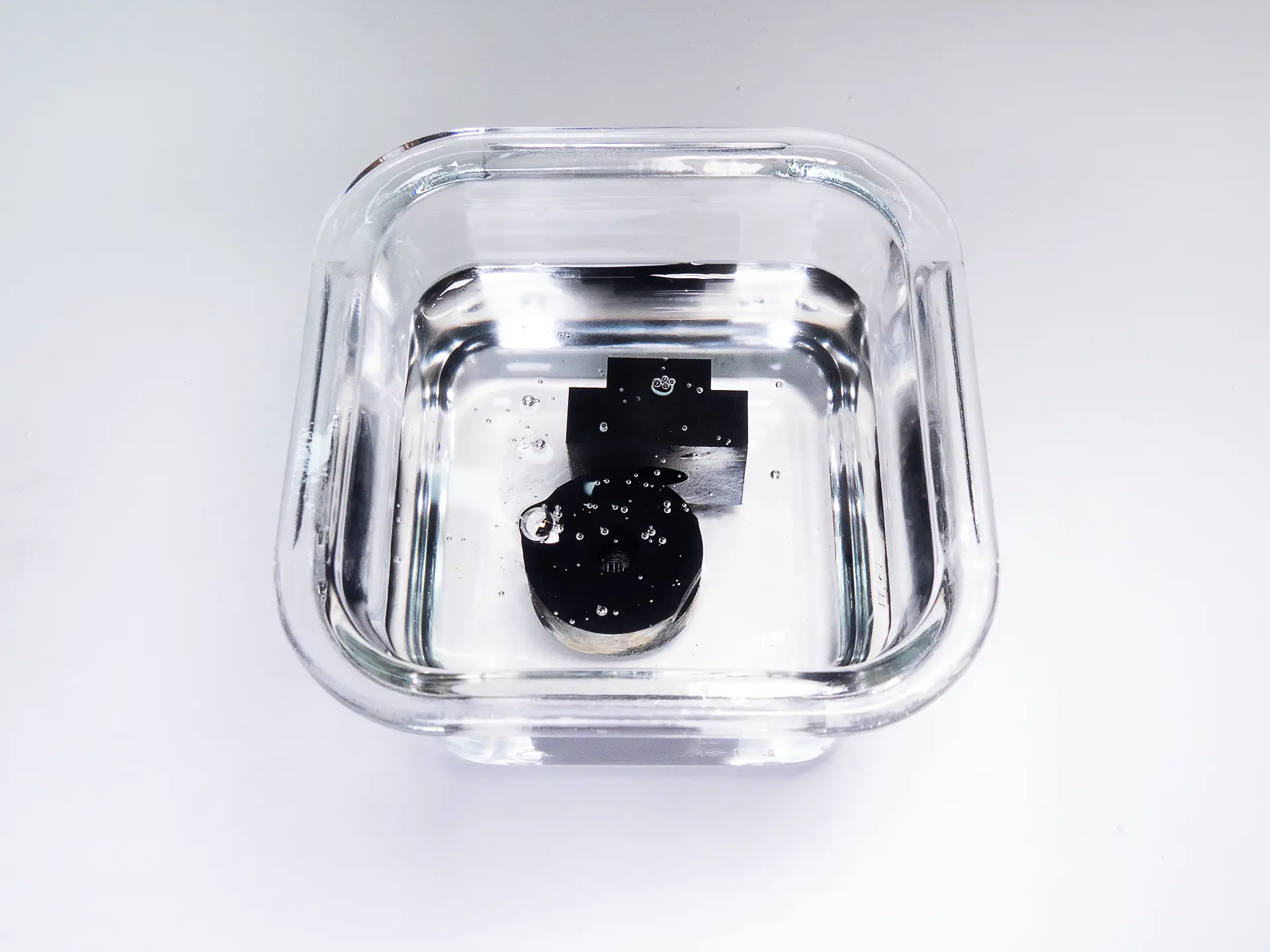
OILING: Soaking in component IV serves to displace water from the blued object and and to seal the bluing layer. In addition, residues of water and bluing fluid are removed.
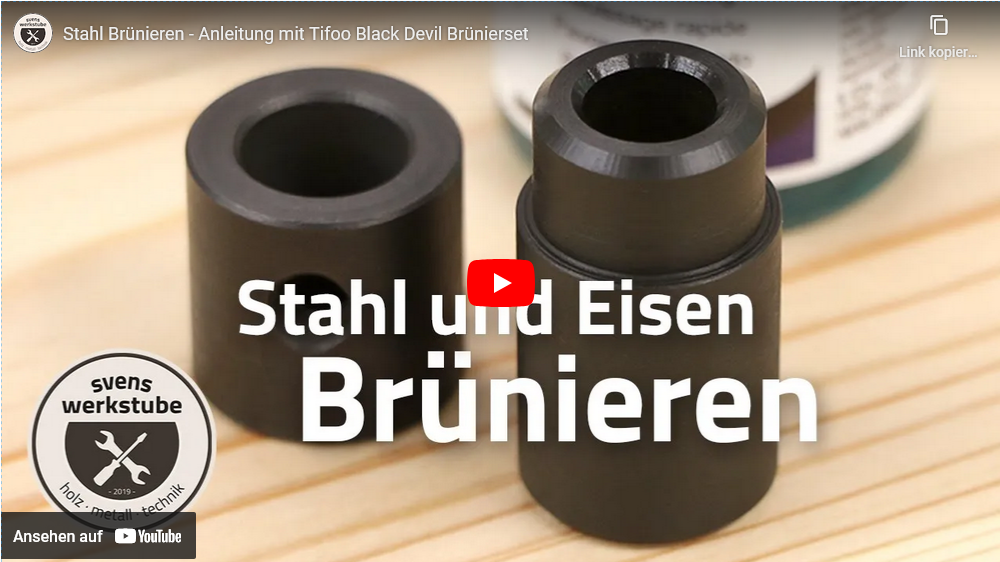
Subsequently blacken immovable parts or repair existing blued surfaces with "Black Magic" quick bluing solution
Blackening aluminium and stainless steel - set up for every metal with our most recent bluing liquids!
Frequently asked questions
Our bluing agents primarily create a black coloured surface that is not a real coating but inhibits the existing surface of steel, stainless steel or aluminium. Corrosion protection is only achieved if the blackened layer is oiled or painted at the end.
This is most likely because the remnants of the bluing agent have not been rinsed off cleanly enough. This causes components of the bluing to crystallise on the surface and form a reddish-brown layer that looks like rust. Make sure that residues of the bluing liquid are completely removed at the beginning and end and that the surface is clean. Repeat the blackening process and wash off the bluing chemical carefully and completely at the end!
Our product range currently allows us to burnish the following materials: Iron, steel, zinc, aluminium and various non-ferrous metals. Check the product detail page for compatibility with the material you have.