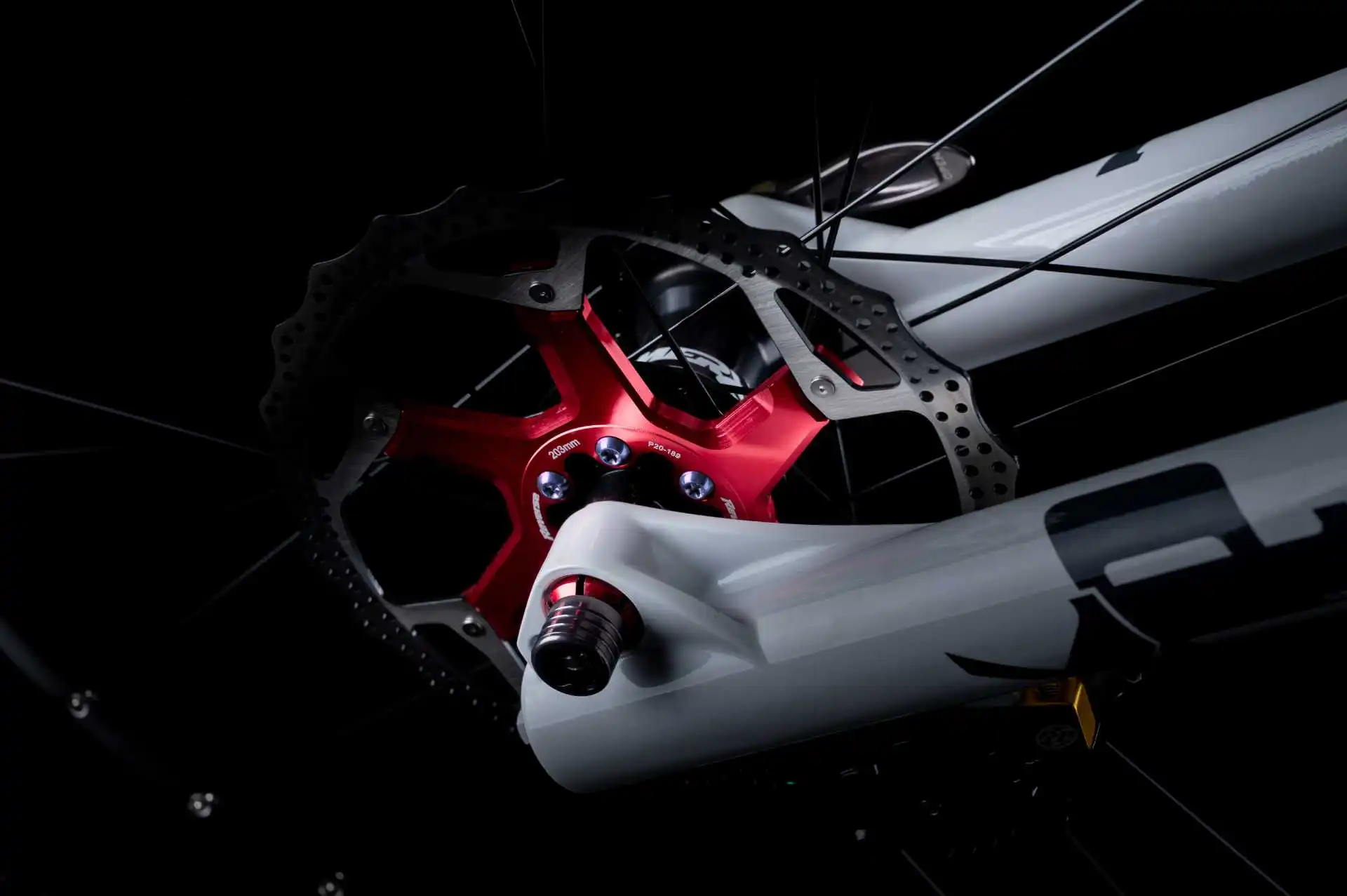
Colourful anodization of aluminium – Electrolytic Oxidation of Aluminium and alloys
Why anodize?
- Protection of aluminium by molecular compound
- Suitable for aluminium and many alloys
- Independent DIY process
- Multiple, combinable decorative colour effects
DIY application
Colouring aluminium surfaces
Protect aluminium from corrosion
Anodizing explained in one video. Find more info on anodizing in our [guide].
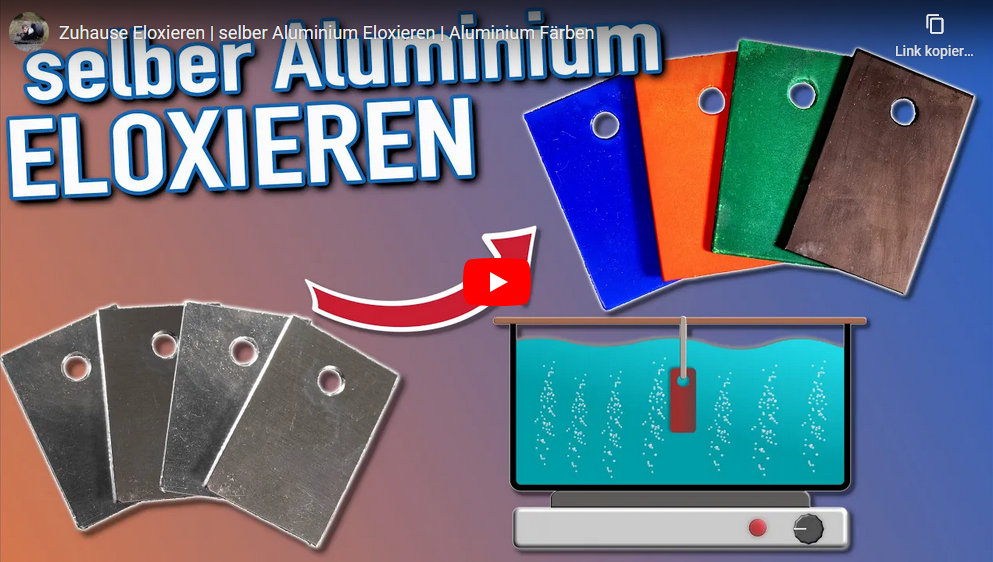
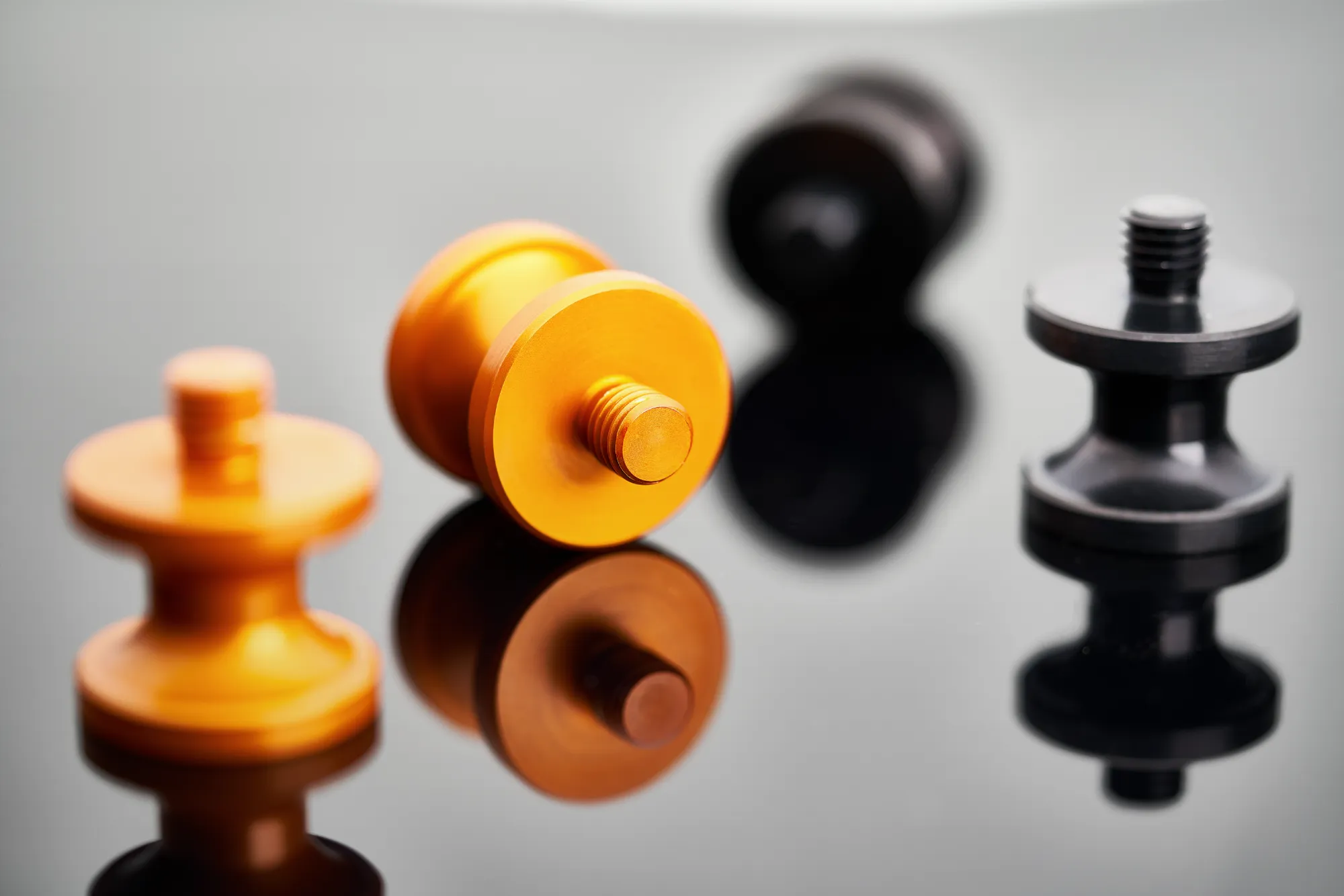
What exactly is anodizing or anodising?
What is the point of anodising yourself?
- With the help of anodising, aluminium surfaces are hardened.
- Anodising process makes the surface corrosion-resistant and longer lasting
- Aluminium is protected by molecular bonding
- Colour storage possible during the process with different anodising colours
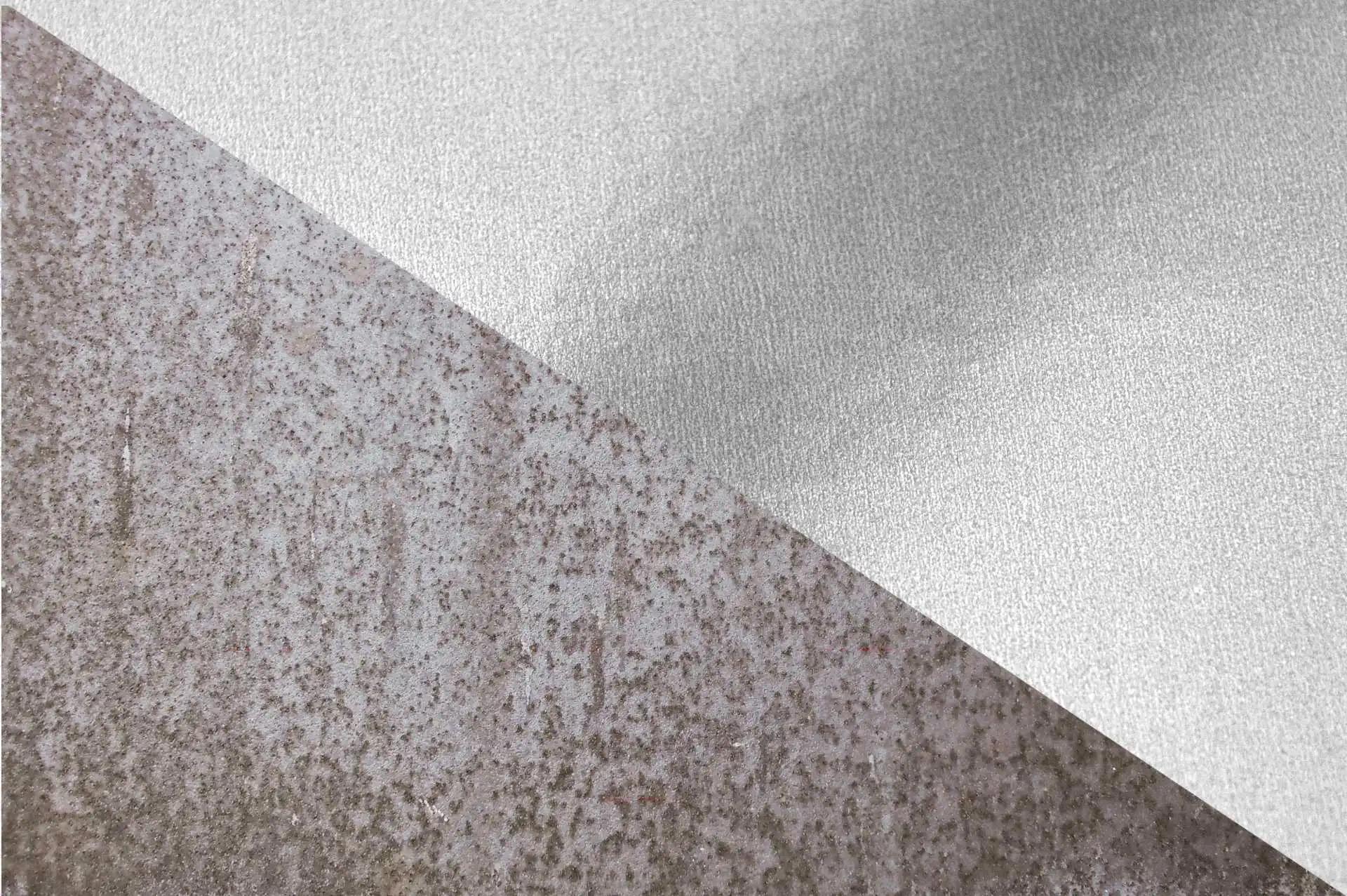
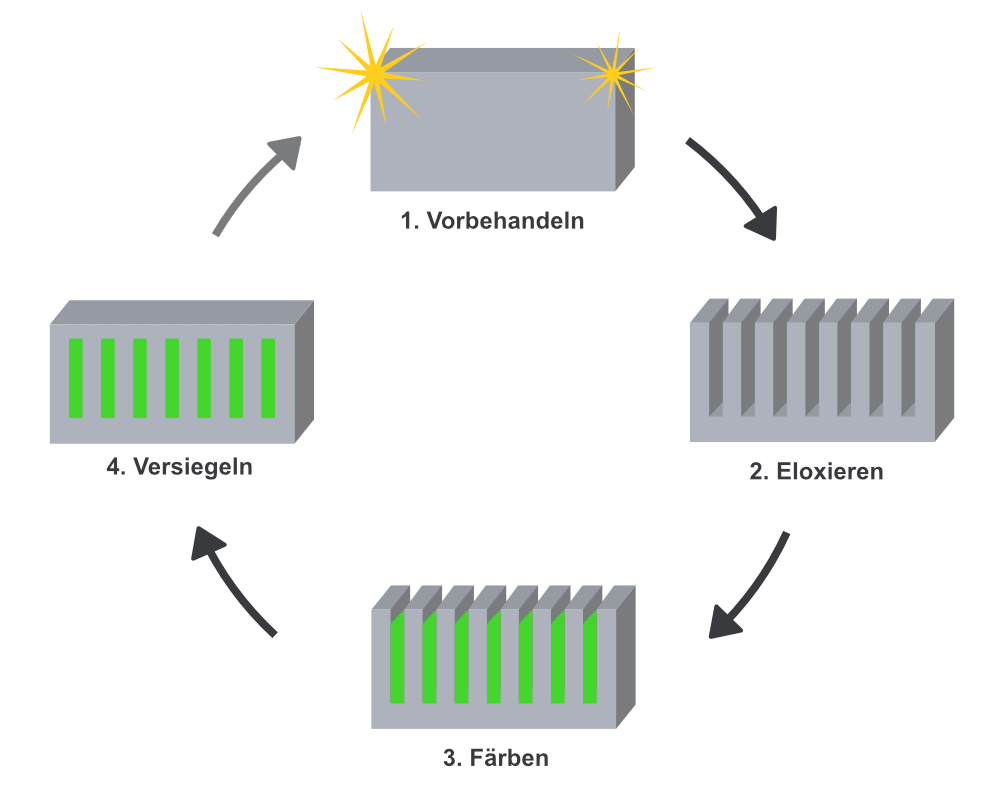
The anodising process essentially involves 4 steps – rinse with water between each step:
- Pre-treatment: For optimal results, the right pre-treatment is crucial. For mechanical pre- treatment, the work piece is polished - for chemical pre-treatment, our products help.
- Anodising: In this step, the actual anodising process takes place, in which the aluminium work piece is anodised in the galvanic structure. As soon as the current flows, water is decomposed through electrolyses on the cathode. On the anode, the oxygen reacts with the aluminium and an oxide layer is formed.
- Colouring: During oxidation/anodising, pores are created on the aluminium surface which allows anodising colours to be deposited in this step.
- Sealing: In the last step, the pores of the work piece are sealed by boiling off. If colour has been deposited, it is firmly sealed into the surface.
It's all in the mix! The more anodising powder, the better.
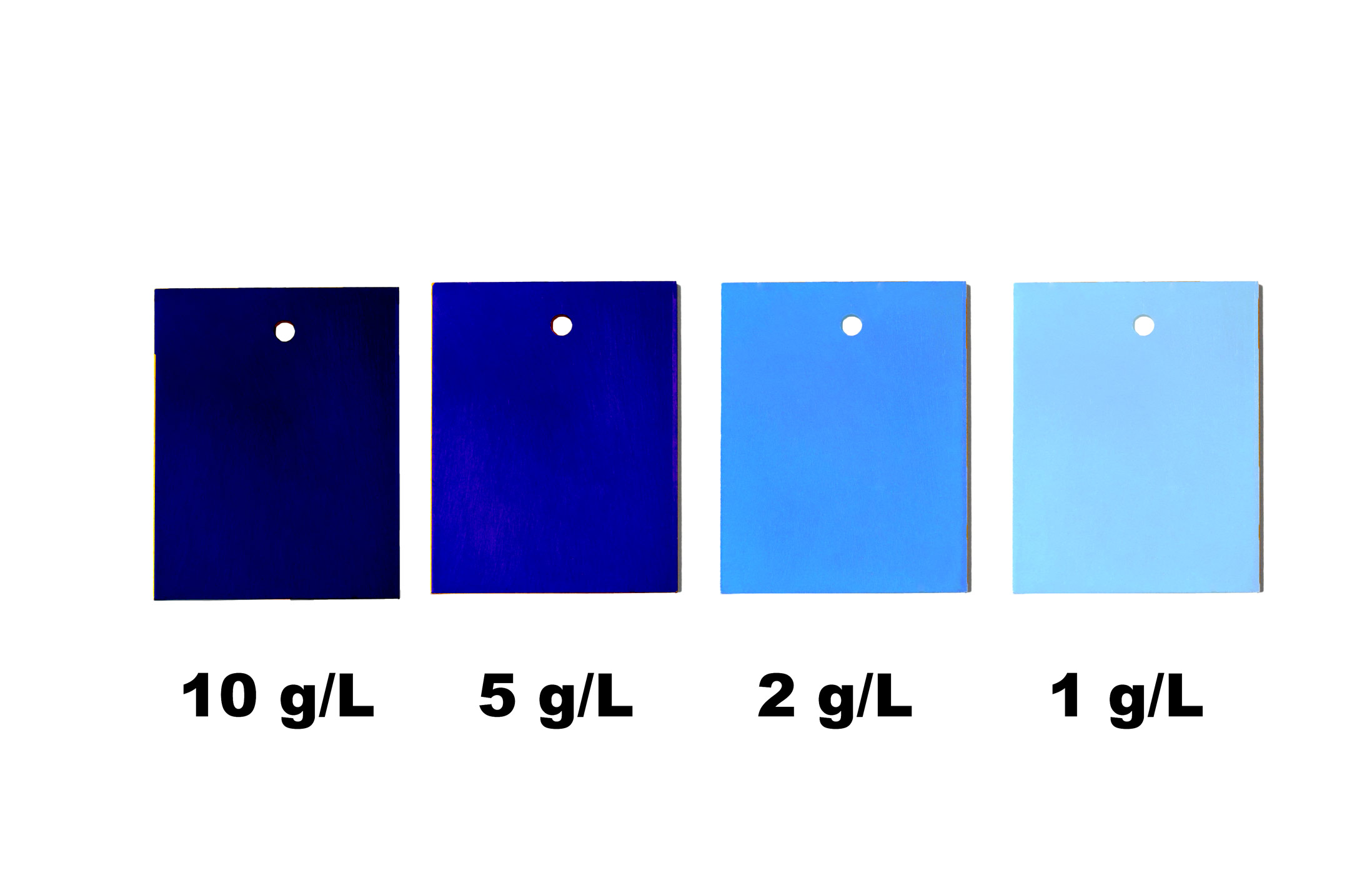
Frequently asked questions
Aluminium and titanium are suitable for anodising. We recommend our products exclusively for aluminium.
Our products cover the majority of the most common aluminium alloys. However, the industry is constantly evolving. For an overview table of compositions suitable for anodising, please see our anodising guide.
In this case, the concentration of the colour solution is not high enough. We recommend 10g/L. Also possible: the alloy is not or only insufficiently suitable for anodising. You can find an overview table on this in our instructions for anodising.
When anodising, the surface area of the workpiece is calculated in dm² and multiplied by 1.5. This gives the necessary amperage for your project. As soon as you set this on your machine, the voltage regulates itself automatically.
No. Only the aluminium piece and titanium wire may be immersed in the solution with the anodising bath. The alligator clips must not come into contact with the bath.